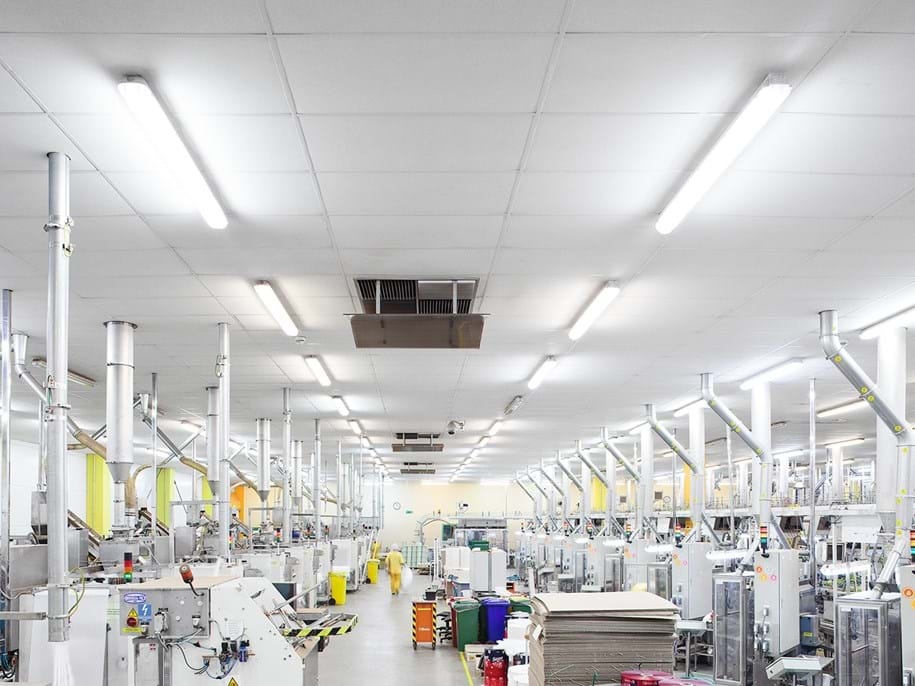
Creating a quieter, safer workplace at Unilever Katowice
In today’s fast-paced industrial environments, noise is more than just a nuisance – it’s a health and productivity issue. At the Unilever Katowice plant in Poland, sound management has become a cornerstone of workplace design. Through smart acoustic solutions and a commitment to employee wellbeing, the company is setting new standards for what a modern, people-first factory should sound like.
Why sound matters in the workplace
In Poland, a healthy work environment is seen as a smart investment. At Unilever, this belief is deeply embedded in how the company design and operate its facilities.
“As a global company, we must lead by example,” says Barbara Oko, Project Engineer at Unilever Katowice. “Workplace wellbeing is a core part of our brand. That includes managing sound levels effectively.”
Meeting and exceeding EU standards
Polish regulations, aligned with EU directives, require hearing protection when average noise levels reach 85 dB. If levels exceed 80 dB, employers must explore ways to reduce exposure.
At Unilever, they go further. The company work with expert acousticians from Laboratorium Acoustic at the Technical University in Wrocław. Together with Ecophon – specialists in acoustic ceiling and wall systems – they design sound-conscious spaces from the ground up.
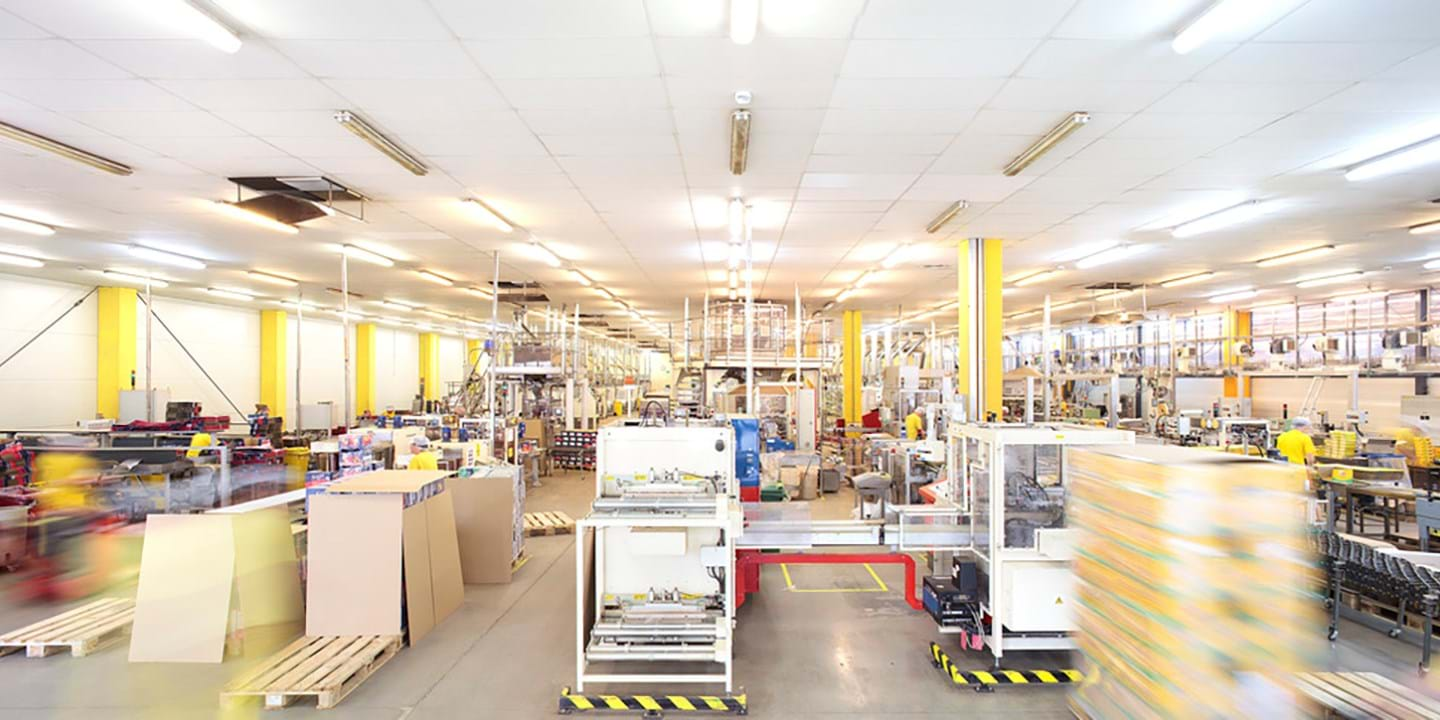
In the tea factory, the installation of a Class A acoustic system – offering the highest level of sound absorption – reduced the equivalent sound pressure level to 78–79 dB(A), safely below the threshold considered hazardous by regulatory authorities.
Inside the Katowice plant
Barbara takes us on a tour of the Katowice site, which spans 6.5 hectares and employs around 900 people. One highlight is the tea factory, built in 2006, where Barbara led much of the project.
“It still feels brand new,” she says. “The acoustic ceiling not only reduces noise but also reflects light, making the space feel bright and fresh.”
Acoustic modelling during construction predicted sound pressure levels could reach 85 dB(A) without treatment. But by installing high-performance acoustic systems, levels dropped to 78–79 dB, with occasional peaks at 81 dB – well within legal limits.
“Thanks to the sound absorbers, we are now below 80 decibels,” Barbara notes with satisfaction.
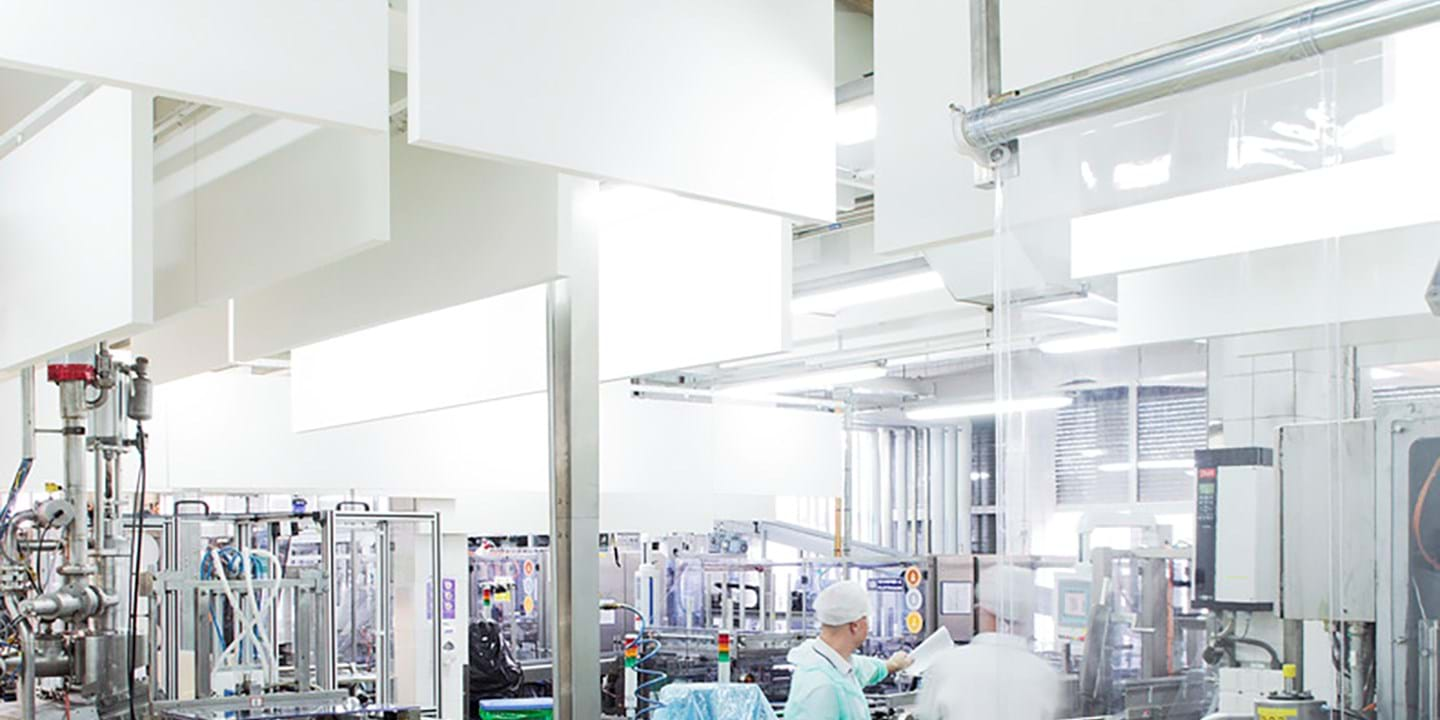
Sound absorbing baffles with a dirt resistant, cleanable surface was the hygienic, room acoustic solution that reduced the sound pressure levels by 40-50% in the margarine factory.
Sound levels cut by half
In the margarine factory, 240 ceiling-mounted sound baffles, Ecophon Hygiene Foodtec™ Baffle C3*, were added in 2010. The result? A 40–50% reduction in sound pressure levels.
“And we’re not stopping there,” Barbara adds. “We’re exploring additional solutions, like free-hanging absorbers above noisy machines, to reduce levels even further.”
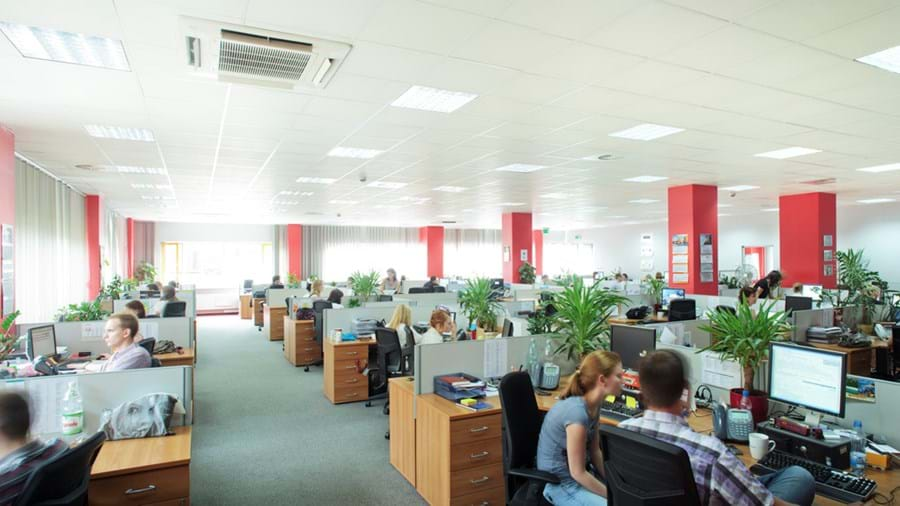
The logistics centre also benefits from acoustic improvements – especially in its two open-plan offices with 120 employees.
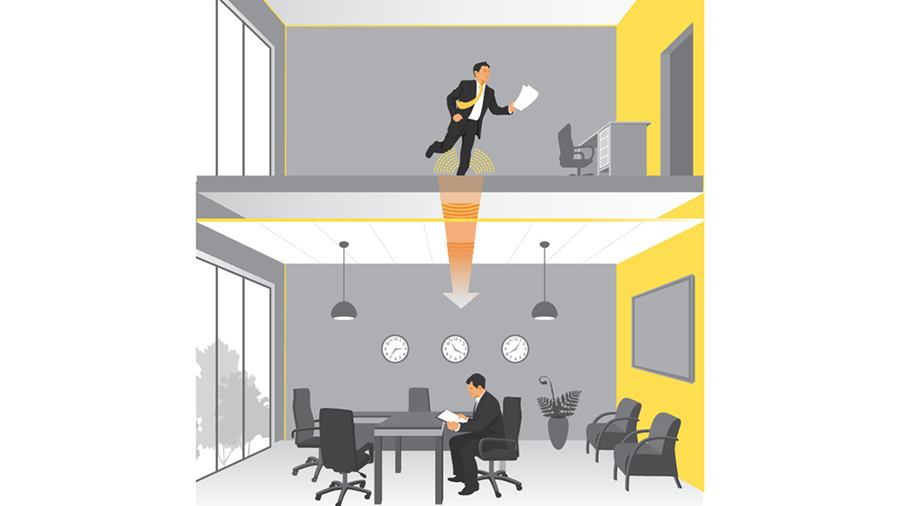
The acoustic system on the ground floor of Unilever’s logistics centre includes impact sound insulation, effectively reducing disruptive noise from the floor above.
A better environment for everyone
The logistics centre, which handles orders across Europe, also benefits from acoustic improvements – especially in its two open-plan offices with 120 employees.
“People have noticed the difference,” Barbara says. “A quieter environment means less stress, fewer mistakes, and better overall wellbeing.”
At Unilever Katowice, sound isn’t just a technical issue – it’s a people issue. And by investing in better acoustics, the company has created workplaces that are not only safer but also more pleasant and productive.
*The product has been updated and is now available under a different name: Ecophon Hygiene Performance™ Baffle.